MCC SERIES ( Catalytic Converter)
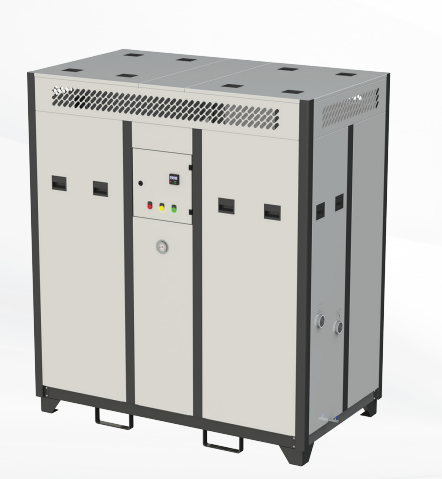
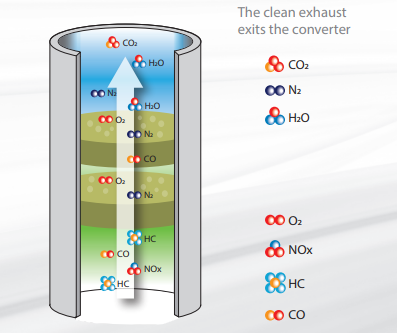
Oil-free compressors are seen as the ideal solution for any application that requires oil-free air. For this reason, the majority of compressed air users prefer to install an oil-free compressor in their system.
However, oil-free compressors are more costly than their oil lubricated counterparts and do not necessarily deliver truly oil-free compressed air. Like all compressors, oil-free compressors can deliver what they receive from the ambient air. In industrial environments the ambient air typically contains between 0.05 to 0.5 mg/m3 of oil (hydrocarbons). When this atmospheric (ambient) air is compressed to 7 bar, the oil concentration output level of the oil-free compressor increases to between 0.4 and 4 mg/m3. This could not be considered oil-free air and will be a problem for the site if oil-free air is a strict requirement.
Mikropor has a more cost-effective solution to minimise compromises in a compressed air system with the new MCC Catalytic Converter. The MCC eliminates residual oil in compressed air by means of a catalytic reaction between the oil-laden air and the reactant (catalyst).
Mikropor’s Catalytic Converters use a process of catalytic oxidation to actively transform the oil and hydrocarbons in compressed air and convert them to H2O and CO2 by utilizing a special type of catalyst.
Mikropor is delighted to present MCC which can be used as a perfect technical solution to obtain an oil-free compressed air system for a wide variety of industries. MCC Catalytic Converters deliver Class 0 oil-free compressed air in accordance with the ISO 8573-1 International Standard.
Oil content in compressor outlet air is reduced to less than 0.0025 mg/m3 by using heat-reactivated catalyst.
Advantages
Mikropor’s MCC Catalytic Converters have less investment & operating cost compared to oil-free compressors and provide;
- Cost reductions (By investing in an oil-flooded compressor with an MCC rather than using an oil-free compressor
- Maintenance cost reductions
- Extended filter change periods
- Eliminated additional costs for separating oil condensate
- Avoidance of costly production standby and shutdown
- Consistent air quality which will remain at the same level for the lifetime of the catalyst
- Extended service life of downstream equipment
- Reduced energy consumption (maximum 0.01 kWh/m3 at maximum load)
Technical Structure Of MCC Series Catalytic Converter
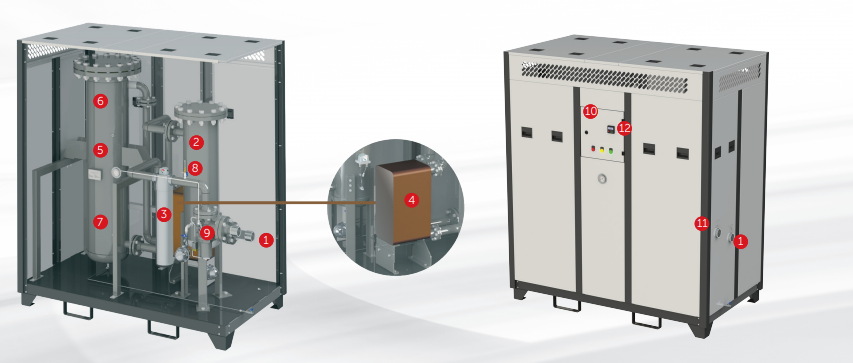
1. Compressed Air Containing Oil From Compressor
2. Mist Eliminator
3. Particulate Filter
4. Heat Exchanger
5. Converter Vessel
6. Heater (Inside the Tank)
7. Catalyst (Inside the Tank)
8. Oil Indicator
9. Minimum Pressure Closing Valve
10. Electrical Enclosure
11. Oil-Free Compressed Air to Dryer
12. Controller User Screen
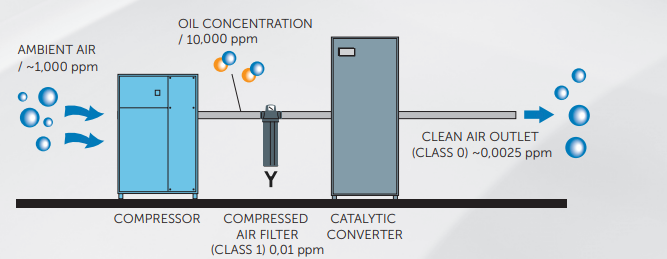
Basic Working Principle of MCC Series Catalytic Converter
At the first stage, specially designed catalyst in MCC vessels is heated up to a certain temperature. The oily inlet air gets resolved into hydrocarbons when entering the heated up container. These hydrocarbons are converted into water and carbon dioxide by reacting with oxygen molecules on the catalyst surface.
Thereafter, completely oil free Class 0 compressed air gets cooled by a heat exchanger and delivered right into the system without the need for any additional treatment.
Oil Indicator
Most users would like to be sure that they deliver oil free compressed air
to their processes. The oil indicator which is standard on MCC Catalytic
Converters proove that there is no oil in the compressed air after the MCC Catalytic Converter.
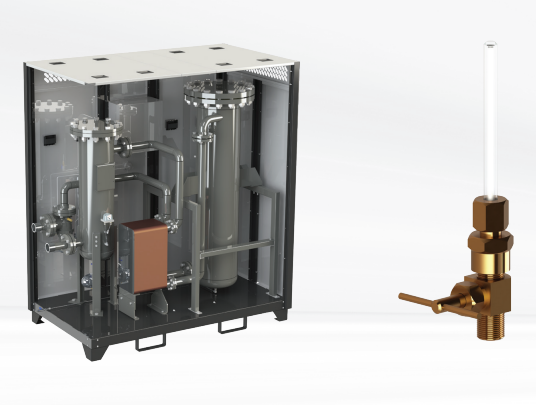
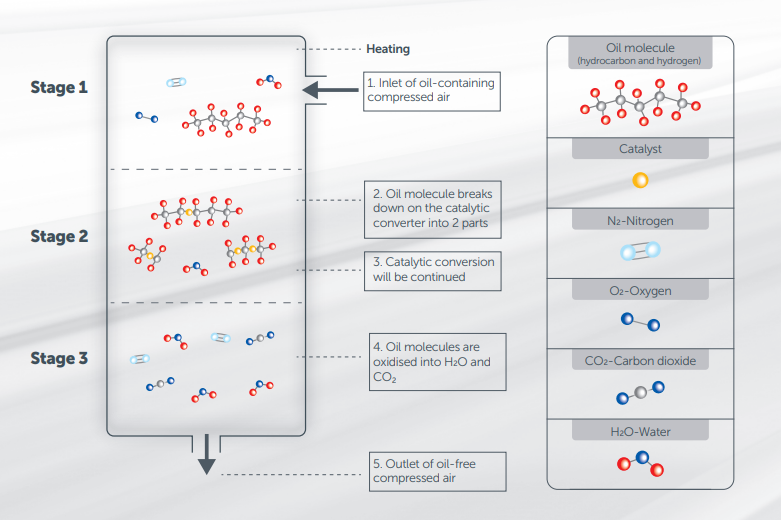
Components are Needed to Design an Oil-Free Class 0 Compressed Air System
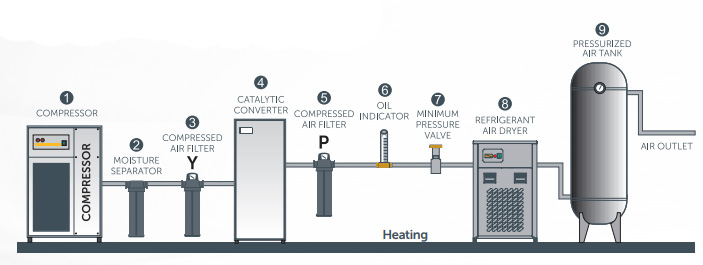
Technical Specifications
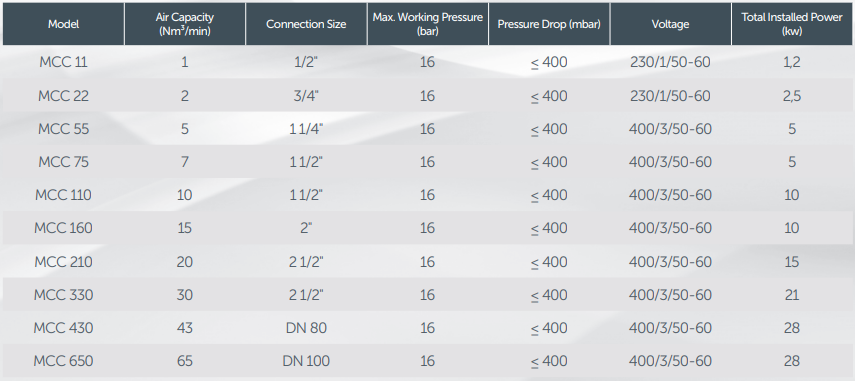