MBS SERIES
High-quality compressed air is highly important for many industries, as it has a vital impact in the breathing air applications. Mikropor breathing air purifiers are designed to eliminate hazardous substancesin the air conforming to related standards. (Mikropor Breathing Air Purifiers are designed for protection against a range of contaminants that may be present in a compressed air fed breathing air system.)
Why Should Purify Compressed Air ?
In systems using compressed air, the ambient air is fed to the compressor. The polluted compressed ambient air remains in the system as long as the incoming air polluting components are not removed.
Where Would You Use Breathing Air Purifier?
Hazardous air pollutants can be released to environment with several applications in various industries. In these industries, it is crucial to eliminate the air pollutants.
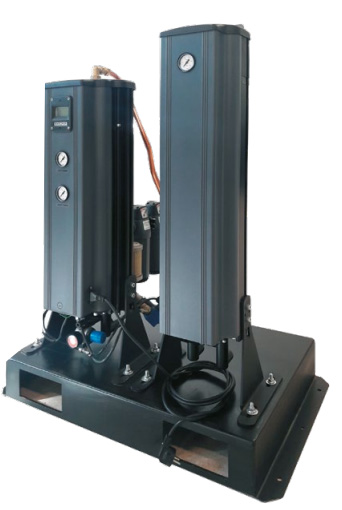
Application Areas
- Shot-blasting
- Spray painting
- Tunnelling
- Confined spaces
- Welding
- Asbestos removal
- Tank cleaning
- Pharmaceutical manufacturing
- High-pressure cylinder filling
- Hospitals
International Breathing Air Standards
The atmospheric air breathing by livings is composed of approximately 78 percent nitrogen, 21 percent oxygen, and 1 percent with small amounts of many other trace components such as argon, hydrogen, and carbon dioxide. In this regard, for the high-quality breathing air, there are relatively standards including the allowable limits of the specification for each component in the breathing air system.
The Breathing Air Purifiers produced by Mikropor comply with the international standards, correlatively.
- OHSA Grade D
- NFPA-99
- CSA Z180.1-00
- CGA G7.1-1997
- EN 12021
- BS 4275
- European Pharmacopoeia
- EN ISO 7396-1:2016
- ISO 14971
Working Principle
1st Step: Water and the oil droplets in the compressed air separated with help of the moisture and particle separators down to 1 micron.
2nd Step: Removing water and oil vapour down to 0.01 mg/m³ with Mikropor Mist Eliminator
3rd Step: Reducing with a heatless desiccant dryer of moisture content to a pressure dew point of -40°C / -40°F, removing any risk of condensation, bacteria, and mold growth.
4th Step: In HOX unit oil vapour and odour are eliminated with activated carbon granules and, CO gas in the air is converted to CO2 down to 0.003ppm with the catalyst granules in the unit.
5th Step: Removal of the remaining dust particles down to 0.01 micron.
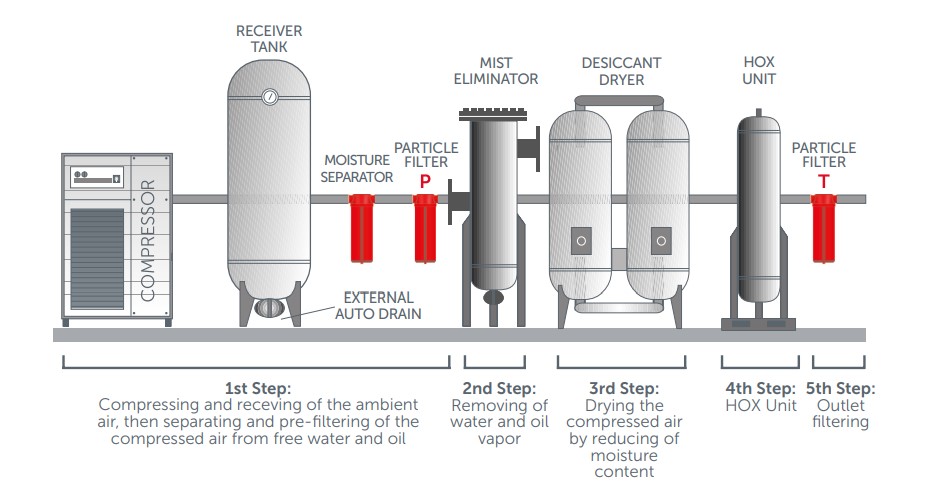
Desiccants and Catalysts for Removal Impurities
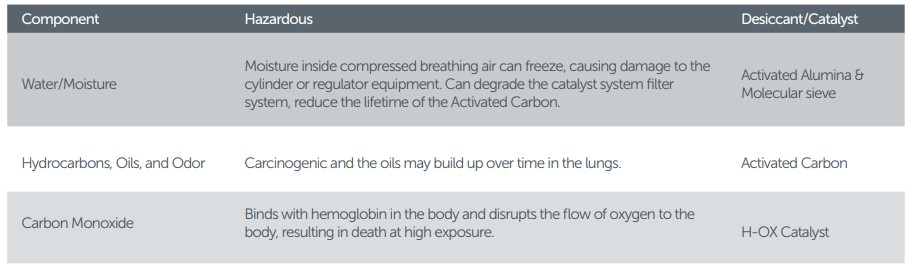
Technical Specifications
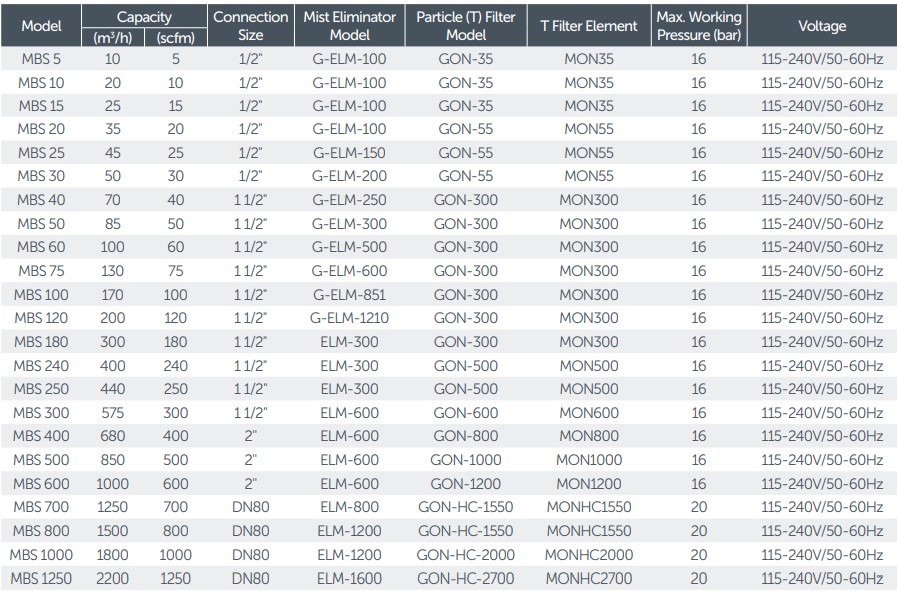